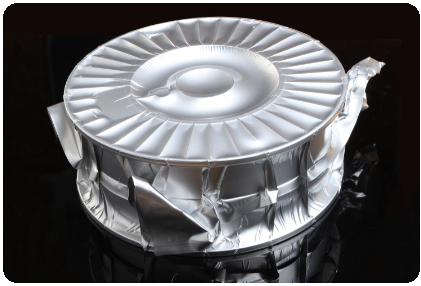
AWS A5.20 E71T-1C
Flux-cored welding wire is a type of welding consumable that is used in the process of flux-cored arc welding (FCAW). It consists of a metal wire with a hollow core filled with flux materials. The flux serves multiple purposes, including shielding the weld pool from atmospheric contamination, providing a protective slag layer, and facilitating the transfer of alloying elements to the weld metal.
TOKO AWS A5.20 E71T-1 welding wires generally produce welds with a softer arc and sharper looking weld than some of the other mild steel wires. Since it can be used for all-position welding, it greatly simplifies the setup process since the parameters can stay the same regardless of the angle of the weld. It also has good feedability characteristics even when using longer wires. Depending on the condition of the welding environment, it may require slight adjustments to the voltage, wire feed speed and amperage.
Flux-cored arc welding (FCAW or FCA) is a semi-automatic or automatic arc welding process. FCAW requires a continuously-fed consumable tubular electrode containing a flux and a constant-voltage or, less commonly, a constant-current welding power supply. An externally supplied shielding gas is sometimes used, but often the flux itself is relied upon to generate the necessary protection from the atmosphere, producing both gaseous protection and liquid slag protecting the weld. The process is widely used in construction because of its high welding speed and portability.
Applications:
Attentions before of Welding:
1. The oil stains and rust on the weldments should be cleared away before
welding.
2. Shielding gas flow rate: 20-25L/min during welding.
3. Designed for welding with 100% CO2.
4. Interpass temperature controlled lower 150℃
for multi pass welding.
5. Storage : Vacuum packaging less than 12 months, other packaging less than 6
months.
AWS A5.20
E71T-1C Typical Mechanical
Properties of Weld
Metal
(kgf/mm2)
(kgf/mm2)AWS
A5.20 E71T-1C Flux-cored welding wire offers several advantages over other welding processes, such as higher deposition rates, increased welding speed, and better tolerance to dirty or rusty base materials. It is commonly used in various industries, including construction, shipbuilding, automotive, and manufacturing..
available grades: AWS A5.20 E71T-GS, E71T-5C, AWS A5.20 E71T-11 etc.
AWS A5.20
E71T-1C 1.2MM
Typical Chemical
Compositions (%)
C
Mn
Si
S
P
Cr
Ni
Mo
Balance
0.045
1.30
0.35
0.011
0.012
0.02
0.01
0.02
---
Yield Strength (N/mm)
Tensile Strength
(N/mm2)
Elongation(%)
Reduction Area(%)
Impack
Value
(J/℃)
480 (49)
550 (56)
29
69
65J / -20℃
Available Sizes and recommended Current Ranges |
|||
---|---|---|---|
Diameter (MM) |
1.2MM | 1.6MM | |
Current (Amp) | Flat | 120~300 | 180~450 |
Vertical Up/Overhead | 120~260 | 180~280 | |
Vertical down | 200~300 | 250~300 |
TOKO Flux Cored Welding Wire is a reliable and high-performing welding consumable that offers exceptional welding properties, versatility, and cost-effectiveness. Its use can significantly improve the quality and efficiency of welding operations. Download AWS E71T-1C MTC and MSDS.
The information contained or otherwise referenced herein is presented only as “typical” without guarantee or warranty, and TOKO Corporation expressly disclaims any liability incurred from any reliance thereon. Typical data and Test results for mechanical properties, deposit or electrode composition and other properties were obtained from a weld produced and tested according to prescribed standards, and should not be assumed to be the expected results in a particular application or weldment. Actual results will vary depending on many factors, including, but not limited to, weld procedure, plate chemistry and temperature, weldment design and fabrication methods. Users are cautioned to confirm by qualification testing, or other appropriate means, the suitability of any welding consumable and procedure before use in the intended application.