Copper Alloys
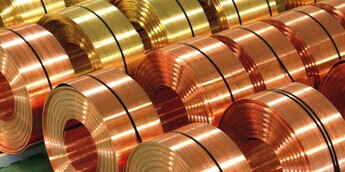
Copper alloys are metal alloys that have copper as their principal component. They have high resistance against corrosion.
Common copper alloy C2600,C2680,C2720 and Oxygen Free High Conductivity
Copper (OFHC) C1100, C1010, C1020 etc.
Features: High intensity ratio of copper (brass, but in general, it is the lowest), electrical conductivity, thermal conductivity, and water in the atmosphere has high corrosion resistance and good plasticity, easy-to-cold, hot pressure processing, easy-to-welding , forging, and tin, no stress corrosion cracking tendencies.
Shapes-Available:in variety of shapes such as: foil, sheet, plate, strip and round rod.
Features: High intensity ratio of copper (brass, but in general, it is the lowest), electrical conductivity, thermal conductivity, and water in the atmosphere has high corrosion resistance and good plasticity, easy-to-cold, hot pressure processing, easy-to-welding , forging, and tin, no stress corrosion cracking tendencies.
Shapes-Available:in variety of shapes such as: foil, sheet, plate, strip and round rod.
Titanium Alloys
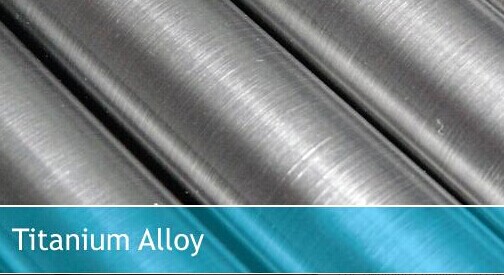
Titanium alloys are metals that contain a mixture of titanium and other chemical elements. Such alloys have very high tensile strength and toughness (even
at extreme temperatures). They are light in weight, have extraordinary corrosion resistance and the ability to withstand extreme temperatures.
Applications: titanium is alloyed with small amounts of aluminum and vanadium, typically 6% and 4% respectively, by weight. This mixture has a solid solubility which varies dramatically with temperature, allowing it to undergo precipitation strengthening. This heat treatment process is carried out after the alloy has been worked into its final shape but before it is put to use, allowing much easier fabrication of a high-strength product.
Shapes-Available:in variety of shapes such as: foil, sheet, plate, strip, bar and rod.
Applications: titanium is alloyed with small amounts of aluminum and vanadium, typically 6% and 4% respectively, by weight. This mixture has a solid solubility which varies dramatically with temperature, allowing it to undergo precipitation strengthening. This heat treatment process is carried out after the alloy has been worked into its final shape but before it is put to use, allowing much easier fabrication of a high-strength product.
Shapes-Available:in variety of shapes such as: foil, sheet, plate, strip, bar and rod.
Aluminum Alloys
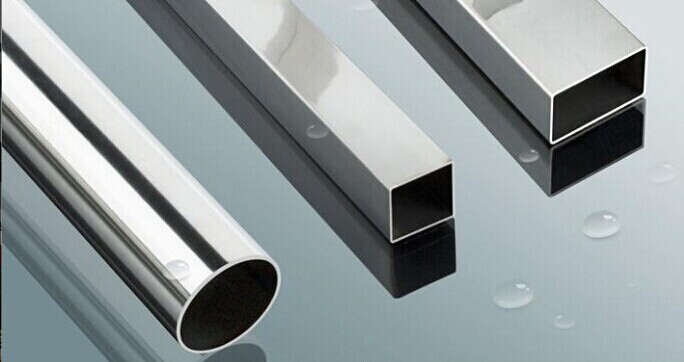
Aluminum alloys are alloys in which aluminum (Al) is the predominant metal. The typical alloying elements are copper, magnesium, manganese, silicon, tin and zinc.
There are two principal classifications, namely casting alloys and wrought alloys, both of which are further subdivided into the categories heat-treatable and non-heat-treatable. About 85% of
aluminum is used for wrought products, for example rolled plate, foils and extrusions. Cast
aluminum alloys yield cost-effective products due to the low melting point, although they generally have lower tensile strengths than wrought alloys. The most important cast
aluminum alloy system is Al, where the high levels of silicon (4.0?3%) contribute to give good casting characteristics.
Applications: Aluminum alloys are widely used in engineering structures and components where light weight or corrosion resistance is required.
Shapes-Available:in variety of shapes such as: foil, sheet, plate, strip, bar and rod.
Applications: Aluminum alloys are widely used in engineering structures and components where light weight or corrosion resistance is required.
Shapes-Available:in variety of shapes such as: foil, sheet, plate, strip, bar and rod.
Al-Sc Master Alloys
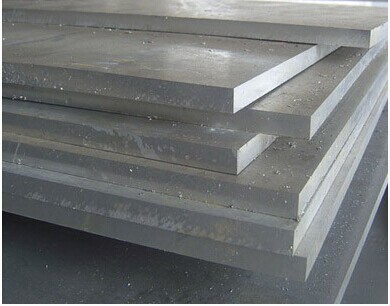
Scandium Aluminum Alloys the main application of metallic scandium by weight is in
aluminum-scandium alloys (Al-Sc alloys) for minor aerospace industry components. The addition of scandium to
aluminum limits the excessive grain growth that occurs in the heat-affected zone of welded aluminum components. Scandium can
significantly increase strength and reduce grain size. Such as: Aluminum-2% Scandium Master Alloy Ingot(98%Al + 2%Sc).
Applications: -For minor aerospace industry components. The common content is 2% scandium. -Another application is scandium-aluminum alloys can be used in some sports equipment, including baseball bats, lacrosse sticks, as well as bicycle frames and related components.
Applications: -For minor aerospace industry components. The common content is 2% scandium. -Another application is scandium-aluminum alloys can be used in some sports equipment, including baseball bats, lacrosse sticks, as well as bicycle frames and related components.