CNC Slitting Line
A CNC slitter, or cut-to-width line, slits coils (steel, copper,aluminium) into precise widths and rewinds them into finished rolls. The process includes coil feeding, precision cutting, packing, and release, ensuring consistent, high-quality output.
iTOKO’s Slitting Machine:
Designed for automation, energy efficiency, and reliability, iTOKO’s machines
feature:
-
Automated controls for minimal manual operation.
-
Energy-efficient systems to reduce costs.
-
Precision blades and tension control for flawless cuts and winding.
-
Modular designs customizable by winding type (center/surface), drive systems (servo/hydraulic), and tension technology.
Thickness | 0.12 ~ 25.0mm |
Width | 300mm ~ 2500mm |
Coil weight | 10, 15, 20, 25, 30, 35, 40, 45Ton |
Cutting type | Drive-cut, Pull-cut |
Cutting accuracy | 0.05 ~ 0.1mm |
Line speed | 80m/min, Max. 300m/min |
Materials | Mild steel, HGI, GI, CCI, CR, HR, SS, Copper, Aluminum |
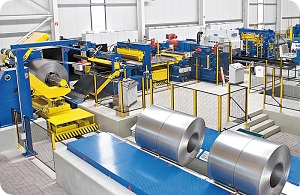
CNC Cut to Length Line
iTOKO’s CNC-driven system cuts coiled materials (metal, plastic, composites) into precise lengths using a shearing mechanism—an upper blade slices against a fixed lower blade for burr-free, high-tolerance cuts.
Process Stages:
-
Coil feeding → Precision shearing (CNC-controlled, ±0.1mm accuracy) → Automated stacking → Packaging → Controlled release.
Features:
-
Programmable CNC controls for rapid adjustments.
-
Durable, quick-change hardened blades.
-
Energy-efficient hydraulics (30% less power).
-
IoT integration for predictive maintenance.
Designed for automotive, construction, and appliance sectors, iTOKO’s line ensures high productivity, minimal waste, and seamless factory integration.
What's advantges from TOKO cut-to-length Line(CTL line)? The general specifications are same as below:
Thickness | 0.15 ~ 25.0mm |
Width | 500mm ~ 2500mm |
Coil weight | 10, 15, 20, 25, 30, 35, 40, 45 Ton |
Cutting length | 500 ~ 6,000mm(12,000mm) |
Cutting accuracy | 0.05 ~ 0.10 |
Leveler | 4 & 6 High leveler(Cassette) |
Line speed | 30m/min ~ 150m/min |
Number of cutting | 10cpm ~ 80cpm |
Cutting type | Rotary, Up-Cut, Fly-Die-Set(DDS) |
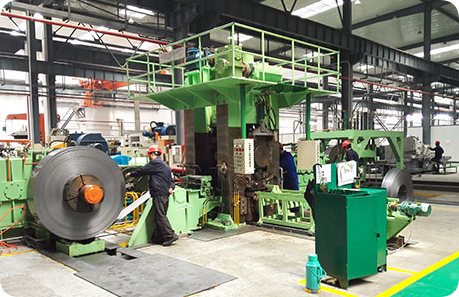
Cold Rolling Mill
iTOKO’s cold rolling mill processes metal sheets, strips, or coils at room temperature to achieve precise thickness, superior surface finishes, and enhanced strength via work hardening. Designed for metals like carbon steel, stainless steel, aluminum, and copper, it ensures high-precision output for industries such as automotive, aerospace, and electronics.
Key Features:
-
Dual-Driven Rolls: Work and backup rolls minimize deflection for ±0.001mm thickness accuracy.
-
Dynamic Shape Control: Adjusts roll pressure to eliminate defects (edge waves, buckles).
-
High-Speed Automation: CNC-driven systems optimize productivity and reduce waste.
-
Mirror-Like Finish: Precision-ground rolls ensure flawless surfaces.
Applications:
-
Ultra-thin gauges for electronics, automotive panels, and aerospace components.
-
High-strength strips for construction and specialty alloys.
Advantages:
-
Superior dimensional accuracy and surface quality vs. hot rolling.
-
Energy-efficient design with IoT-ready monitoring.
iTOKO’s mills deliver precision, durability, and adaptability for high-performance metal production.
Photo Gallery
- High Speed Slitting Line (0.6~4.0) x 1600MM
- High Speed Slitting Line (1.0~6.0) x 2000MM
- High Speed Slitting Line (0.8~6.0) x 1600MM
- High Speed Slitting Line (2.0~8.0) x 2000MM
- High Speed Slitting Line (0.4~5.0) x 1600MM
- High Speed Slitting Line (0.6~2.5) x 700MM
- Heavy gauge Cut-to-Length"CTL" line (2.0~10.0) x 2000MM
- Heavy gauge Cut-to-Length"CTL" line (2.0~12.0) x 2100MM
- Light gauge Cut-to-Length"CTL" line (0.12~1.4) x 1250MM
- Light gauge Cut-to-Length"CTL" line (0.6~5.0) x 1500MM
- Light gauge Cut-to-Length"CTL" line (0.3~3.0) x 1600MM
- 850MM,Five-Stand Continuous Steel Cold Rolling Mill
- ERW steel Pipe/Tube mill (25.4~89mm) x (0.8~4.0mm)